Share
Pin
Tweet
Send
Share
Send





Trabalhar na mesa trouxe muito prazer. O pedido do meu cliente foi especial (e interessante). E como um estímulo - o orçamento. Sua solicitação incluía os seguintes itens:
- - Bancada com bordas sem arestas de ambos os lados, composta por duas placas de nogueira separadas.
- - Muitos padrões e contraste.
- - Cavidades no meio para uma coleção de ágatas.
- - Para iluminar a ágata na cavidade deve estar a luz de fundo do LED.
- - As cavidades são cobertas com inserções de vidro removíveis.
- - As dimensões das bancadas têm 100 cm de largura e 210 cm de comprimento.
- - Pernas de aço personalizadas (sombreadas).
- - Um banco em um estilo semelhante.
- - O tempo de produção não é superior a um mês.
Tentei documentar todas as etapas do processo, mas os prazos eram bastante apertados e, às vezes, não tive a oportunidade de tirar uma foto. Desculpe pelas fotos ausentes; Vou tentar descrever essas etapas com mais detalhes ...
Pesquisa de material







Não considero esta etapa a principal, mas pode demorar um pouco. Uma parte significativa do tempo foi gasta energia e gasolina em várias serrarias e lojas de madeira em busca de material adequado. Foi como uma façanha, dados os requisitos estabelecidos para a largura. Eu precisava encontrar duas pranchas com arestas brutas e, colocando-as lado a lado, a largura total deve ser de 100 cm. Sua forma deve formar espaços vazios para acomodar a coleção de ágatas do cliente. Os conselhos devem ter padrões pronunciados característicos. Ainda havia requisitos padrão: as tábuas eram secas no forno ou por alguns anos no ar, tinham uma aparência agradável, um avião sem torcer desnecessariamente, deformar, cortar (tudo o que exigiria a remoção da camada de espessura). E, claro, o custo deve ser razoável.
A pesquisa geralmente começa com os sites classificados eletrônicos na seção de materiais de construção. Freqüentemente, artesãos locais colocam à venda pranchas extras a preços razoáveis. As lojas também podem colocar anúncios, tentando atrair mais clientes. Encontrei várias opções decentes nas proximidades, mas não havia nada que satisfizesse todos os requisitos. Depois disso, olhei para alguns lenhadores locais que viram toras em tábuas. Esses caras costumam ter suas próprias serrarias e vendem a prancha a um bom preço, porque obtêm os toros mais baratos ou de graça, e a qualidade nem sempre é a mais alta. Mas essa opção também não funcionou, então tive que passar para as lojas e armazéns. Obviamente, uma escolha já apareceu aqui, mas a um preço muito alto.
Finalmente, encontrei o que precisava em uma loja local. Não é realmente na loja. Descobriu-se que seu dono tem sua própria serraria e armazém, que é cheio de tábuas com bordas não cortadas. Ele tinha várias pilhas de nozes das quais se podia fazer uma escolha. Aqui encontrei o que estava procurando. As pranchas tinham uma largura ideal, serrada a partir de um tronco (a simetria era preservada), seca nas condições certas por 3 anos, bonita e plana, e o preço era relativamente barato. O bônus foi anexado a eles. Como eles foram tratados com uma plaina larga, eu não precisei eliminar isso moendo uma superfície de serra irregular. Eu não tenho uma plaina de 60 cm de largura ...
Durante a pesquisa, enviei fotos ao cliente para obter sua aprovação. Nós dois optamos pelos dois. Por fim, foi possível avançar para a próxima etapa do projeto!
Desenvolvimento e aprovação do projeto



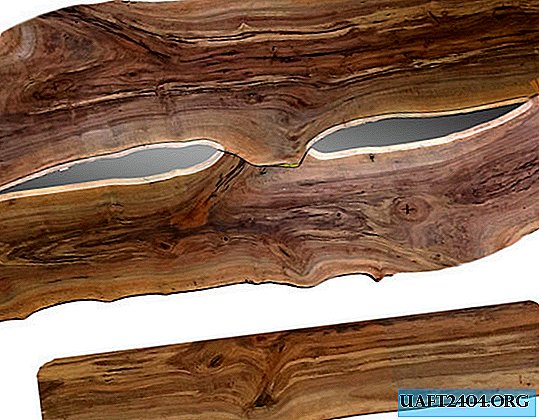



Antes de embarcar em uma ferramenta, quase todo meu projeto começa com o desenvolvimento do design em um sistema de desenho auxiliado por computador (CAD). Com arestas brutas, isso é um pouco mais difícil, pois é difícil repeti-las em CAD. Resolvi o problema, colocando uma escada alta e tirando fotos das tábuas ao longo de todo o comprimento. Depois importou as fotos para o programa e circulou os contornos. Uma fita métrica estava visível na foto para dimensionar com mais precisão os gráficos.
Depois de projetar os modelos eletrônicos, eu os sobreponho com uma imagem real da superfície das placas, para que fosse mais fácil para o cliente imaginar o que eu ia fazer. Depois que decidimos o design, eu projetei elementos diferentes, como eles interagiriam e se uniriam.
Para este projeto, desenhei um vetor de diferentes projeções do modelo para vários propósitos. Ele desenhou os contornos das cavidades centrais e os exportou para um arquivo DXF, que ele enviou à empresa de vidro para que eles cortassem as mesmas formas para mim. Usei o mesmo arquivo para fazer um modelo com um contorno de cavidade, no qual será possível cortar placas de policarbonato que serão montadas na parte inferior da bancada. Cortei padrões e policarbonato na minha fresadora CNC caseira. Também recortei um modelo para fixar partes das pernas de metal para soldá-las corretamente. Até cortei perfis de várias partes metálicas com um laser, o que me ajudará a cortar as partes das pernas no ângulo certo. Depois de projetar o modelo completo em CAD, você pode começar a trabalhar ou, pelo menos, será muito mais fácil trabalhar com ele.
Preparação da placa (massa de trincas, fixação de nós, trituração)




Na maioria dos casos, gosto quando todos os nós, rachaduras e vazios são fixos e preenchidos com resina epóxi preta, principalmente quando se trabalha com nozes. A cor preta costuma parecer natural e, às vezes, dá contraste. Como as pranchas aqui e houve rachaduras bastante profundas, usei resina com um longo tempo de endurecimento; isso permitirá que ele absorva bem e ajude a realmente consertar as rachaduras, e não crie a ilusão de preenchimento. A desvantagem deste método é que quase sempre é necessário aplicar a resina novamente na segunda e às vezes na terceira vez. Às vezes, para reprocessamento, uso uma resina com tempos de cura rápidos. Enchi todos os espaços vazios dos dois lados das pranchas para que pudessem ser firmemente fixados. É melhor aplicar resina epóxi com um "pote" para que não sejam detectadas bolhas durante a moagem (para que elas subam acima do plano da placa).
Depois de preencher todos os espaços vazios, tratei as partes salientes do epóxi com um abrasivo com grãos P60.
Modelagem de juntas

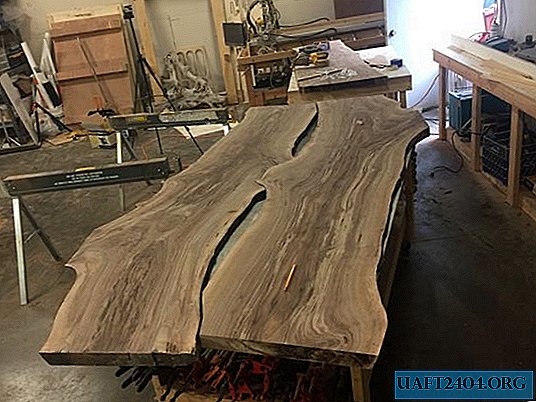










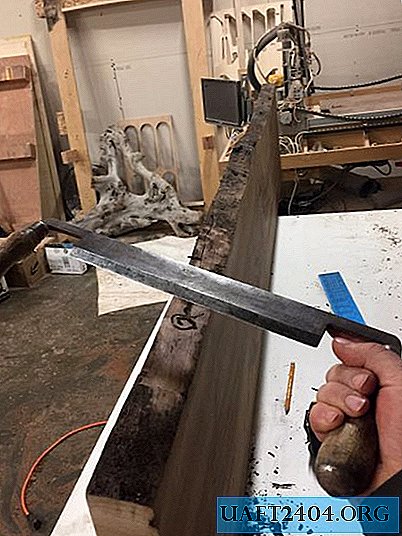


Infelizmente, não documentei essa etapa particularmente. Basicamente, coloquei uma prancha na outra na posição exigida e marquei a área a ser removida. Diretamente para o trabalho, usei uma serra de vaivém, uma rebarbadora (com uma fresa e um disco de aba) e, quando necessário, ferramentas manuais para talhar. Nesta fase, havia muito bom acabamento e adequação. Ao longo de todo o comprimento entre as tábuas, deixei uma costura com cerca de 4 milímetros de espessura. Eu pensei que desta maneira a mesa pareceria mais expressiva. Por outro lado, um ajuste perfeito deixa os cantos, o que não parece muito bom. A espessura da costura será preservada graças à chave de cauda de andorinha. Então alinhei as bordas da mesa com uma serra circular.
Durante esse estágio, esfreguei as bordas ásperas dos resíduos de casca na mesa e no banco. Depois, passei por cima deles com uma rebarbadora com um disco de pétalas, para que as bordas não cortadas fiquem mais lisas.
No banco, cortei um lado cru com uma serra circular. Concordei com o cliente que no banco um lado seria reto.
Unir tábuas com buchas e buchas










Usei cavilhas para conectar as partes centrais. Eles servem para consertar duas pranchas em um plano (em relação uma à outra). A carga principal na fixação das bancadas cairá nas teclas e pernas da mesa. Diferentemente das chaves que encontrei, as fiz com uma espessura quase igual à espessura das tábuas.
O material para as cavilhas foi feito colando uma folha de noz entre duas folhas de mogno e uma máquina CNC cortou um molde. Também fiz um modelo que ajudará a cortar os rasgos de chaveta com uma fresa manual.
Depois de alinhar a costura entre as tábuas, eu as fixei à mesa com grampos. Então, usando o modelo, cortei as ranhuras com uma fresa. Onde a fresa deixou a ranhura arredondada, tive que trabalhar com um cinzel. Você poderia fazer uma cauda de andorinha com arredondamentos, mas eu gosto da aparência de cantos uniformes.
Quando as chavetas estavam prontas, tentei cuidadosamente inserir uma cauda de andorinha (para garantir que não ficasse presa!) E comecei a colar. As cavilhas eram um pouco mais grossas que as ranhuras, então eram lixadas niveladas com a bancada.
Após a conclusão desta etapa, lixei todas as superfícies que se deslocam do grão P60 para o P180. A moagem final com grão P220 foi realizada imediatamente antes do polimento.
Inserto de vidro, policarbonato e LED

















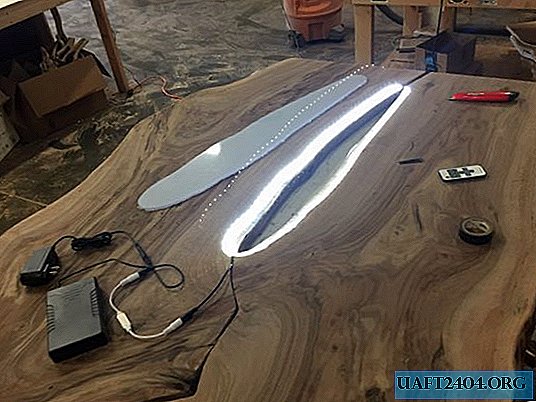








Usei o modelo CAD para criar pastilhas para vidro e uma placa de policarbonato. A fita dupla face é perfeita para fixação temporária de espaços em branco na superfície da mesa. Então, novamente, usei o moinho manual para criar ranhuras nos dois lados das placas. Para um trabalho mais preciso, usei um zenzubel e um formão, até o vidro ficar liso e fixo sem hesitação. O vidro foi removido e inserido várias vezes, para isso usei ventosas.
As pastilhas de uma folha de policarbonato foram preparadas usando uma máquina CNC e uma fresa de topo. Aqui tive que tomar uma decisão sobre como consertar as inserções de plástico com mais segurança na parte inferior da bancada. Eu queria que eles fossem fáceis de remover, por exemplo, para substituição devido a arranhões. Decidi que as caixas de seleção de nozes seriam perfeitas. Portanto, eu os cortei com um cortador a laser do material que tenho.
Antes de inserir o plástico, tive que lidar com a luz de fundo do LED. Para um efeito mais sofisticado, decidi colocar a iluminação LED em torno do perímetro do plástico. Essa técnica também ajudará a esconder os fios. Comprei uma tira de LED fina com um lado adesivo, que pode ser facilmente colado no recesso que fiz anteriormente ao redor da parte inferior da cavidade. Eu tive que montar dois circuitos elétricos separados na forma de Y, que deveriam entrar em um dimmer separado. O dimmer, por um lado, se conecta à bateria e, por outro, com uma fonte de alimentação de 12 volts. Isso permite que as lâmpadas brilhem a partir das baterias e da rede elétrica. A idéia é que os hosts conectem o carregador quando não estiverem usando a mesa e seria possível remover os fios quando eles interferirem. Os fios e a bateria foram presos ao fundo da mesa usando grampos e âncoras. Eu considerei a opção de incorporar a bateria e os fios em uma árvore, mas finalmente decidi que era melhor não, pois todos esses componentes teriam que ser substituídos em algum momento. No final, esta tabela deve se tornar um valor familiar que sobreviverá a mim, ao cliente e às lâmpadas LED. Eles dizem que as lâmpadas LED podem durar muito tempo, mas se houver um desejo, elas podem ser substituídas por algo assim.
Depois de experimentar o plástico e verificar a iluminação, coloquei os pratos de lado. Bandeiras de bloqueio e plástico podem ser afixadas após o polimento.
Polimento














O cliente desejava usar material de polimento, que preservaria a aparência natural da árvore, tornando-a resistente, mas não parecendo verniz. Portanto, decidi pelo OSMO PolyX. Este produto foi projetado para pisos de madeira, mas também é adequado para móveis. Apresenta baixo teor de substâncias orgânicas voláteis e alto teor de sólidos, pois consiste principalmente em cera e óleos naturais. É fácil de aplicar. Para obter um bom resultado, duas camadas são suficientes.
Não tirei fotos desse processo, pois estava constantemente usando luvas de borracha manchadas com pasta de polimento. Antes de aplicar as camadas, caminhei mais uma vez pelas superfícies e bordas com um abrasivo de grão P220.
Para aplicar uniformemente o OSMO à superfície, usei uma espátula. Foi fácil para eles umedecer completamente a árvore e com uma pasta para cobrir todos os pequenos inchaços. Nas bordas eu tive que usar tecido. Depois de molhar, retirei o restante da pasta com um pano sem fiapos. Nesta fase, é importante trabalhar minuciosamente as superfícies, mas remova completamente o excesso. Cobri a parte superior, inferior e todas as bordas da mesa e dos bancos, e os deixei secar por um dia ou dois, depois o fiz novamente. Apenas duas camadas são suficientes e, de fato, se aplicadas mais, isso pode levar a um efeito brilhante indesejável.
Como resultado, o processamento das peças de madeira foi concluído, coloquei as placas de policarbonato em seus lugares e prendi-as com clipes de bandeira.
Criação de pernas e sua instalação






























As pernas foram feitas de um tubo de aço retangular medindo 3,8 x 7,6 cm e 3,8 x 3,8 cm de um canto de ferro. Para facilitar o processo, recortei padrões com um cortador a laser para fixar os componentes necessários e a peça, o que ajudará a juntar tudo no ângulo certo. Era uma vez um grande soldador, mas os anos se passaram e sem prática suficiente eu ainda tinha habilidades funcionais, mas esqueci de cozinhar com costuras decorativas. Para amenizar essa falha, usei uma rebarbadora para retificar o excesso de metal e dar à superfície uma aparência mais elegante.
Após a conclusão do trabalho de soldagem, processei todas as superfícies metálicas com uma rebarbadora com um disco de lâmina, para que tenham uma textura e brilho uniformes. No metal de canto, cortei orifícios retangulares para fixar as bancadas, para que, em caso de compressão ou expansão da madeira, não houvesse problemas. Soldamos as partes inferiores das pernas com chapas de ferro, para fazer furos nelas e instalar um mecanismo de ajuste de altura.
O cliente desejou que as pernas fossem pretas. Nós ponderamos um pouco sobre a melhor forma de fazer isso. Em vez de tinta, decidimos usar um agente de polimento de aço, para que o resultado seja mais estável e oculte melhor as falhas. Eu usei um produto chamado presto black. A aplicação foi realizada através de um spray até que todas as superfícies estivessem cobertas com uma substância e depois neutralizou seu efeito usando uma solução de bicarbonato de sódio, para que o metal não começasse a oxidar (ferrugem). Depois de remover o agente de polimento, sequei o metal com um compressor e cobri a superfície com poliuretano fosco para que não enferruje ao longo da estrada.
Para prender as pernas, usei parafusos e porcas de móveis, o que permitirá remover e instalar as pernas novamente. No banco, fixei as pernas com parafusos de madeira grandes, pois eles não são grandes e podem ser movidos sem remover as pernas.
Entrega e instalação







O cliente vive a três horas de mim, portanto, ao transportar a mesa, era importante embalá-la corretamente. Desconectei as pernas do banco e da mesa, cada componente embrulhado separadamente e colado em material de embalagem plástica. É importante embrulhar e embalar as peças em ordem de desmontagem, pois, quando você as montar novamente, elas estarão no caminho certo. Será mais fácil assim. Por exemplo, quando cheguei na casa onde o cliente morava, a primeira coisa que aconteceu ao descarregar da van foi uma bancada. Coloquei-a na casa de cabeça para baixo no chão. As próximas peças disponíveis foram as pernas que coloquei na bancada. Então o banco, as pernas do banco e assim por diante. Isso pode parecer senso comum, mas se você se empolgar com a embalagem, poderá facilmente esquecer tudo. Não gravei esse processo, mas tenho certeza de que é bastante simples de imaginar.
A cliente gostou muito do conjunto de jantar, e agora nos recantos iluminados encontra-se sua coleção de ágatas, no meio há um buquê para a estação e ao redor de um conjunto de cadeiras especialmente selecionado. Isso está na foto. Uma mesa pode reviver uma sala já adorável.Fico feliz que esta criação caia em uma bela casa onde serão admiradas e cuidadas.
Obrigado pela atenção!
Artigo original em inglês
Share
Pin
Tweet
Send
Share
Send